Glass act
Innovator / Gerhard Baier
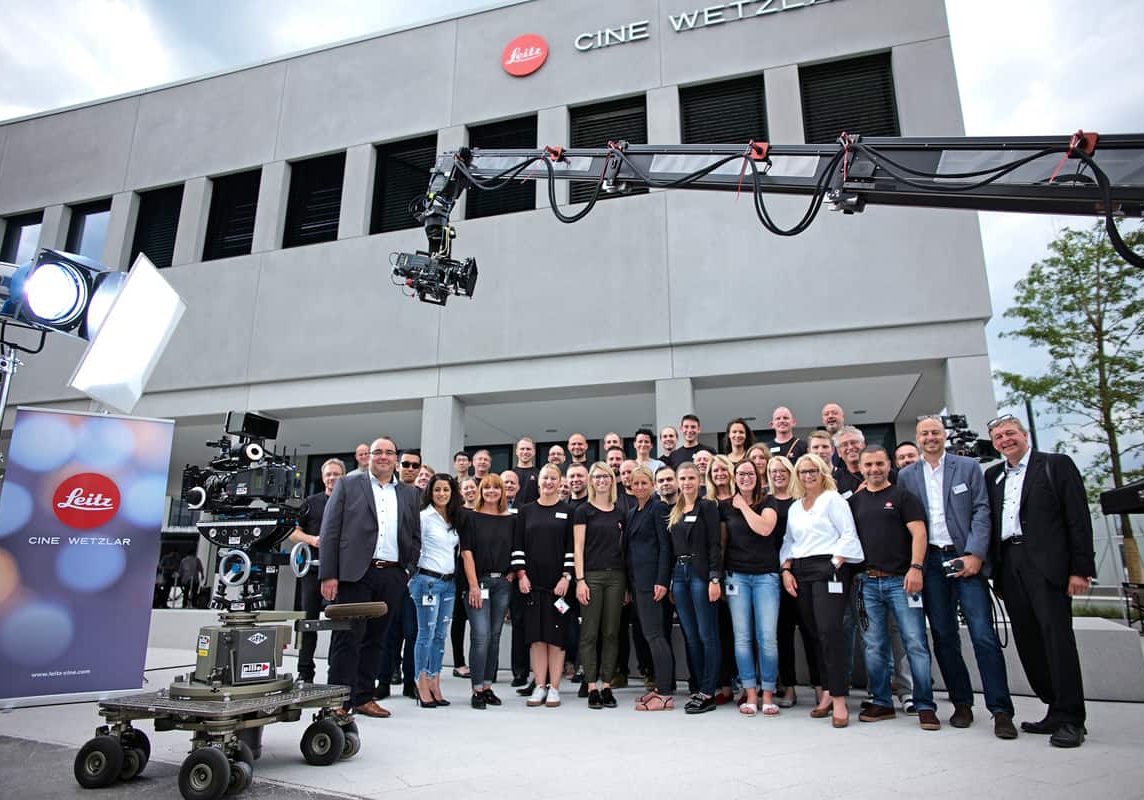
Glass act
Innovator / Gerhard Baier
BY: Michael Burns
The name Leica should need no introduction to readers of British Cinematographer Magazine, but the name Ernst Leitz Wetzlar may be slightly less familiar. It shouldn’t be, though. This, the new name of the CW Sonderoptic lens manufacturing company, is a homage to Ernst Leitz, who created Leica over a century ago in the German city of Wetzlar. In a move that includes a new factory, all new lens orders are being delivered with a new Leitz red dot.
“Until the late 1980s, Leica stills photography lenses bore the name Ernst Leitz Wetzlar,” says Gerhard Baier, managing director of Ernst Leitz Wetzlar GmbH. “The Leica camera in the early days was a product of Leitz company, the Lei-tz Ca-mera. After ten years of CW Sonderoptic, it was the right moment for us to go back to our roots of lens manufacturing and take this heritage into the future.”
CW Sonderoptic – the name was a German translation of ‘Cine Wetzlar very special project in lenses’ – started in 2008.
“For decades, the film industry wanted Leica to do cine lenses,” Baier explains. “There had been quite a few conversions of photo lenses for cine and so on. The cinematographers wanted to pass the look they knew from stills photography into motion, but it never happened in a serial production.”
That is until 2006, when three components came together. The vision of Dr Andreas Kaufmann, a Leica investor, the design team of Iain Neil and André de Winter, and a lens concept originally conceived by photographer and filmmaker Christian Skrein and Hollywood rental house owner Otto Nemenz.
“That was the beginning of the Summilux-C project,” adds Baier. “The Summilux-C lenses deliver something that users know or remember from [classic] photography, where pictures were shot on Leica cameras with Leica lenses. We use the same techniques and processes and adjustment criteria that Leica is using on the stills photography side, but for cinematography.
“Later, we added a second line, the Summicron-C, and of course we needed more people,” he continues. “So now in our tenth year, we have four product lines with Summilux, Summicron, M0.8 and Thalia, and 50 people. When we started planning a fifth and a sixth line, it became obvious that our place was going to be too small. With the creation of the Leitz Park 3 area, with a hotel and a museum, we got the chance to move into a new building and rename the company.”
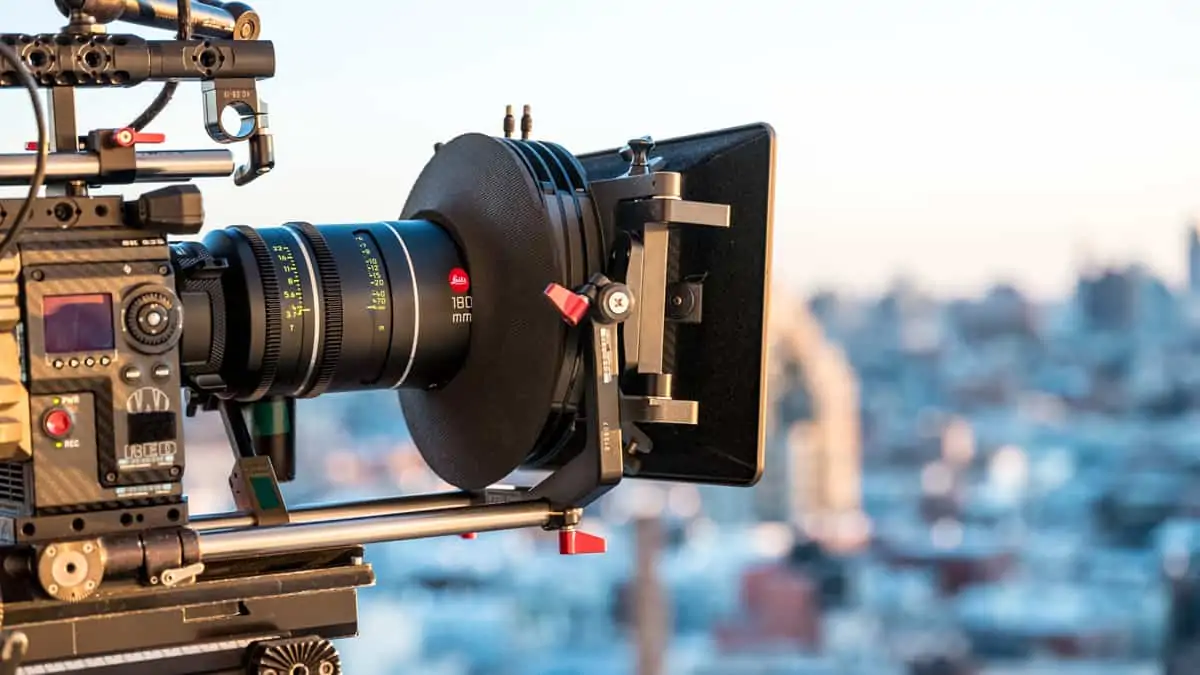
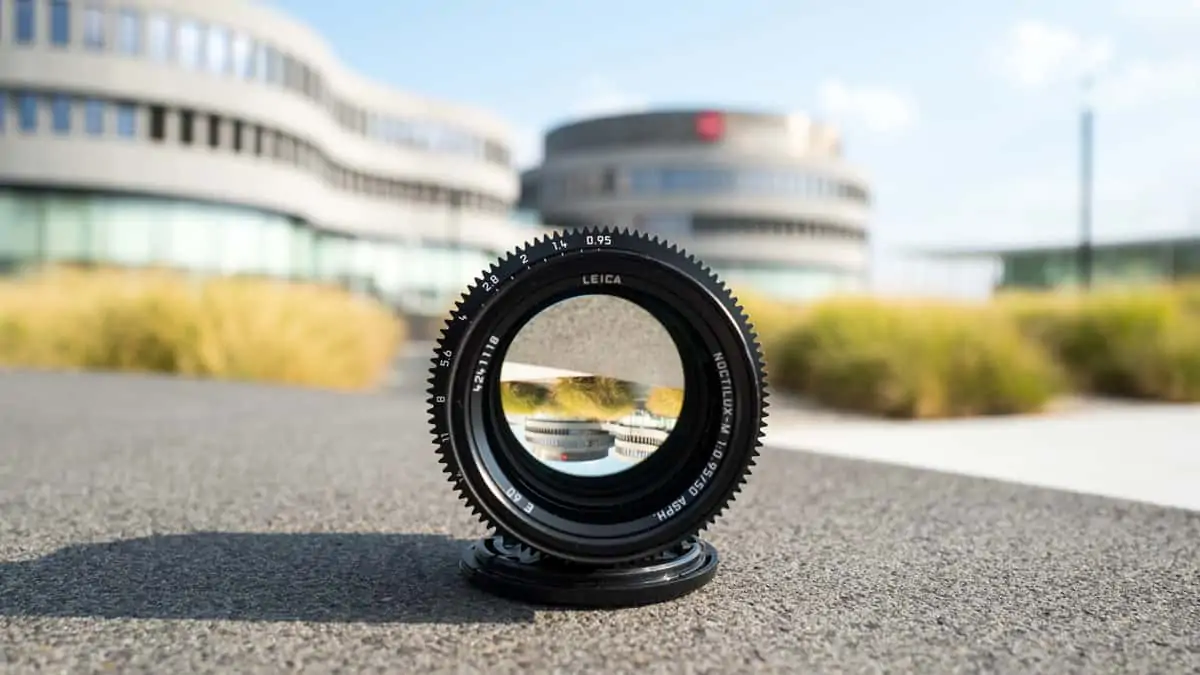
Baier himself has a background in photography and filmmaking, having financed his economics degree at university by working in the photography sector.
“I worked with a master of photography for commercial product shots of all kinds – furniture, electronic components and so on – she taught me a lot about lighting,” he says.
Baier also applied for a position at the university’s new video lab, where he produced scientific movies on 16mm and 35mm movie formats, whilst his interest in theatre groups around that time led to experience in theatre lighting, photography and capturing theatre productions on video.
“When you work in this field, one thing leads to another and I found myself holding a camera for a broadcast production,” he says. “I was hired as an assistant, as second unit camera for industrial movies, commercials, and documentaries. I worked as a war reporter in Bosnia, and finally I got into feature films.”
In the late 1990s Baier returned to university, there building on his film and broadcast experience to gain a master’s degree in Media Science. Following this he returned to Munich and moved into the rental sector for film, video and presentation equipment and later working with Amnon Band of Band Pro Film & Digital.
“I did the first big digital projections, including on waterfalls during the World Expo in Hanover in 2000,” he says. “I produced movies and got a German film award. When digital cameras came to market, I was one of the first to buy the Sony HDW-F900 for rental.”
In 2000, the company partnered with Carl Zeiss to create the DigiPrime and DigiZoom lenses for 2/3-inch chip cameras.
“I moved from the rental house to a sales company,” Baier says. “We became specialists and pioneers in digital cinematography. All this, if I look back, led more or less unplanned to where I am now.
“I joined CW Sonderoptic in early 2012, but was in touch with them for quite a few years before,” he adds. “What I brought to the company was my experience in the wide field of motion picture capture – including an understanding of budgeting for a movie – practical experience while using the product on-set, not in a lab, as well as my long-term relationships in this industry.”
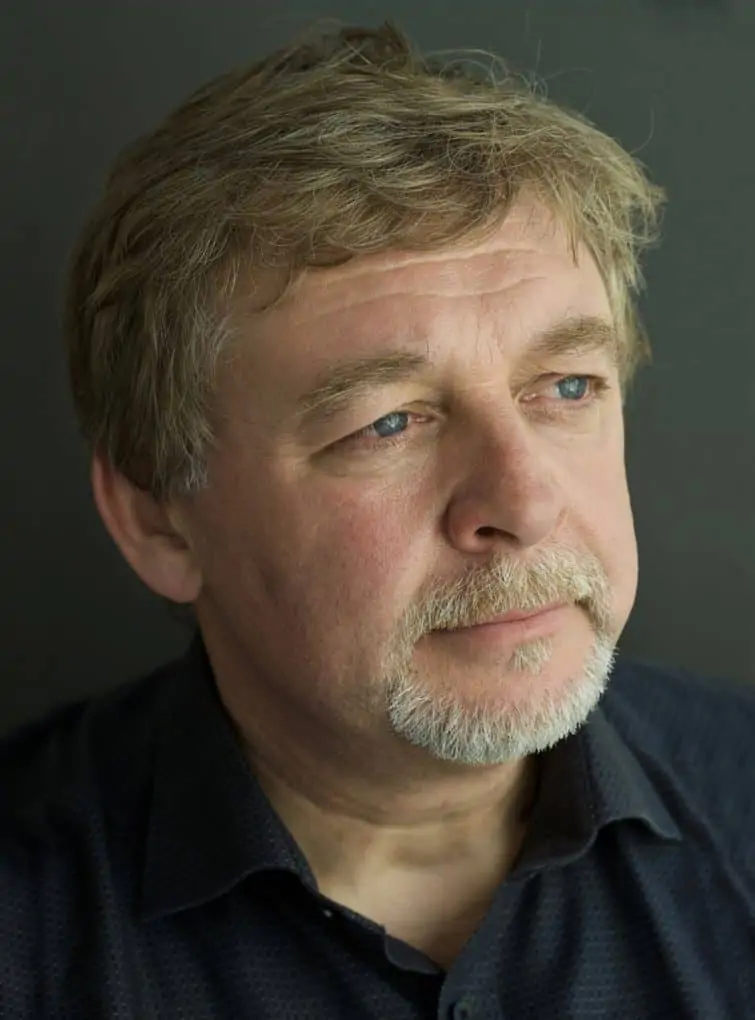
"Cine lens manufacturing is still a lot about experience, craftsmanship and handmade processes. Every lens gets a ‘soul’ and that is partly due to the people that worked on this lens.
I think there is something that is very individual to the lens... You look through and you get a personal feeling that this lens is right or wrong for this specific project."
- Gerhard Baier, MD, Leitz Cine Wetzlar
A normal day for Baier, if there is one, is split between the administration, organisation, resourcing and financial demands of running the factory, and being with the production team. It’s clear the latter is where he feels he can get hands-on: “checking, testing, tweaking lenses, making sure that we get the result we want.
“Of course, we have a lot of machines, but cine lens manufacturing is still a lot about experience, craftsmanship and handmade processes,” he continues. “Every lens gets a ‘soul’ and that is partly due to the people that worked on this lens. I think there is something that is very individual to the lens. Yes, there is a ton of resolution, there is high contrast, no breathing or colour fringing, wonderful skin tones… but you look through and you get a personal feeling that this lens is right or wrong for this specific project.”
“I also travel a lot to exhibitions, to camera associations, and on sets,” he adds. “This is where you find out if what you are doing is right or wrong.”
It’s also here that a lot of his conversations with cinematographers happen. “Usually we talk about images, light and shadow, paintings, and of course the lenses – the eyes of the camera,” he says. “I am always interested in how cinematographers are choosing their tools and why. You look for where the language of film is going to and what this means for optical and mechanical designs.
“This is very useful information for me, because I can see trends in what they are looking for with regards to the imaging language,” he continues. “Then I try to translate this for the engineers into technical terms. You start with a white piece of paper and you put down some preliminary specs, being led from the image and also from the practical operational side. The input here from first ACs is very important. You figure out the focal lengths and how many lenses should be in a set, thinking about the T-stop and if can you achieve this with all focal lengths at the same diameter or where you need to compromise.
“Our head of development is one of the best optical engineers in the world and there is always a fight between what you want, what is doable, what is pushing the physics to the limit, and what is the cost. You achieve a compromise at the best possible level.”
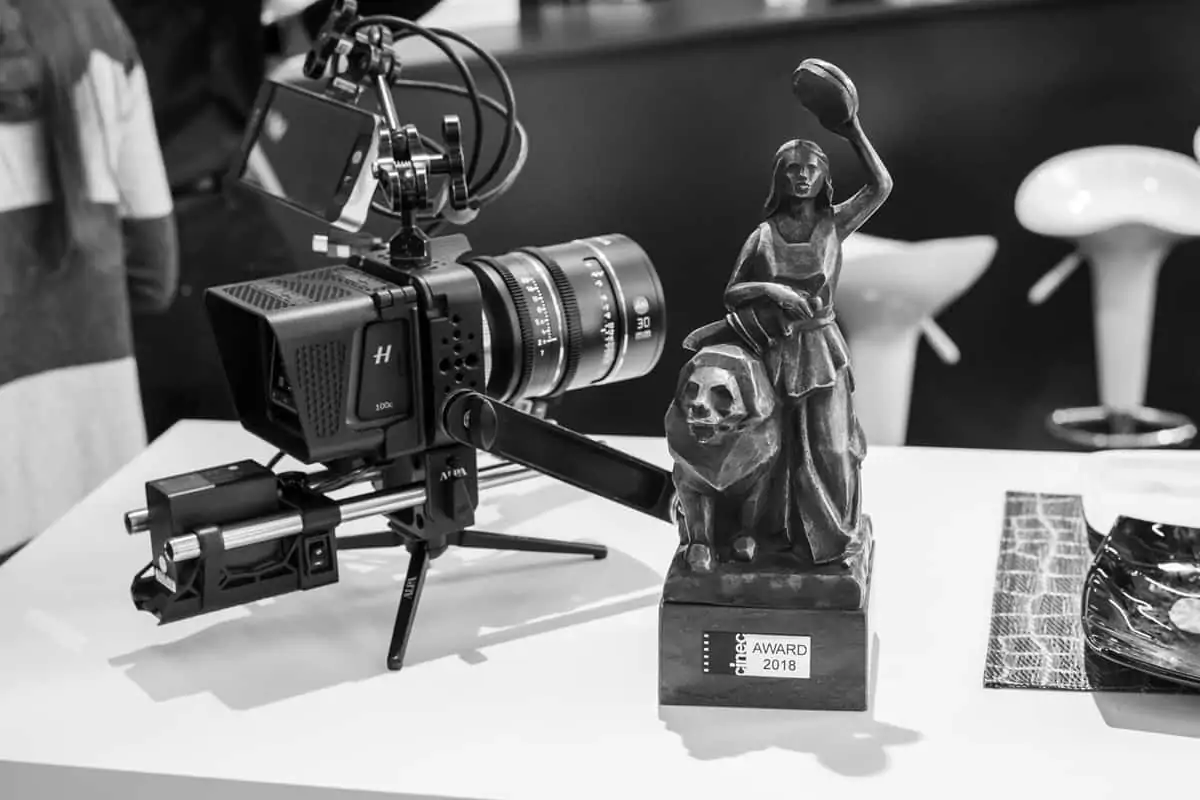
Baier notes that, like his career, the industry seems to have gone from electronics/digital to analogue to digital, and over again. “It’s a very interesting time in this industry, however I am not that sure all these changes are so significant in the end,” he says.
“You still need good stories, good storytelling, an understanding of light and shadow. I just – with my team – make the lenses for this. We will serve the market as best as we can with tools for outstanding images.”