Explore how ARRI’s CPO programme and other innovative solutions contribute to sustainability in production, offering cost-effective, high-quality equipment while reducing environmental impact.
The energy requirements of a product are often seen as an indicator of its eco-friendliness, but there is much more to consider. Eco-friendly design also demands durability, reparability, and the availability of spare parts. Other essential criteria include carbon emissions over production, product lifespan, and disposal to complete a life cycle assessment. New products come with a carbon footprint due to the energy and resources required for their manufacturing. In contrast, refurbished cameras, lenses, and luminaires reduce reliance on primary materials, cut electronic waste, and can be more cost-effective.
The ARRI Approved Certified PreOwned (CPO) programme provides creatives with access to high-quality, cost-effective equipment. ARRI offers refurbished products with the same warranty as new models. DP Lucca Barone-Peters, who purchased a refurbished AMIRA through the ARRI Approved CPO programme, reports, “In the two years I’ve had the camera, I’ve shot more than 50 projects with it, and it hasn’t faltered once. The image continues to be great and holds up well against newer cameras.”
ARRI rigorously inspects and refurbishes products intended for resale. Each product undergoes testing to repair mechanical defects and replace worn parts. Products receive the latest software version and a final functionality test before being certified and released for resale.
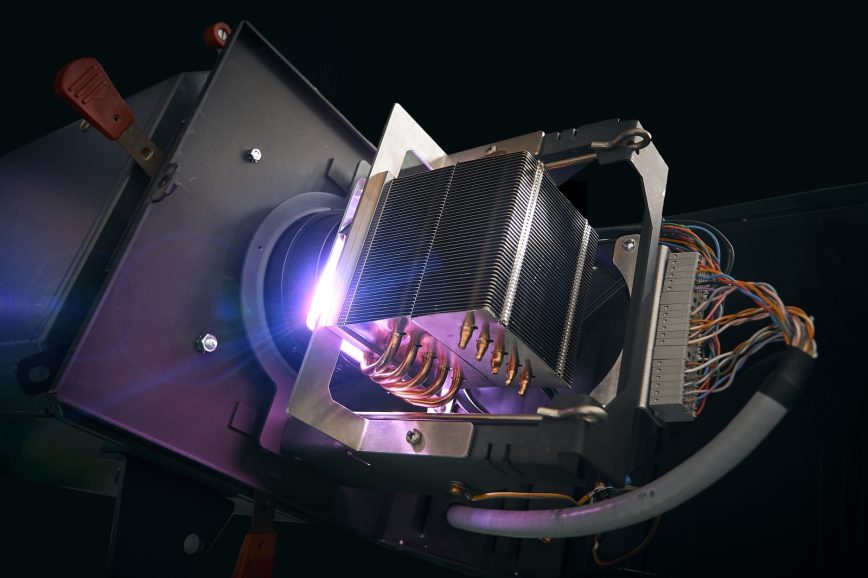
“ARRI facilitates a circular economy by ensuring that all products and services are produced and distributed sustainably,” emphasises Arne Stadler, manager, CPO ARRI Group. “Our CPO programme, software updates, and global service centres support a circular product lifecycle and conserve Earth’s resources.”
Filmmakers, cinematographers, and broadcasters need reliable equipment with a long lifespan. DP Colby Gottert, who bought an Alexa Mini LF through the ARRI CPO programme, initially thought he had shorted out the camera. “The CPO team helped me through it, and I was relieved to realise that the camera was fine. The problem turned out to be a defective third-party battery plate I had bought.”
Every analogue and digital ARRI camera can be repaired as part of the CPO programme, provided that spare parts are available. Spare parts for newer models are guaranteed for many years. “If defects occur in older cameras, especially analogue models, it can be challenging. If spare parts aren’t readily available, the ARRI Service team will try to reproduce or salvage parts from defective cameras,” explains Stadler.
“Opting for the CPO programme is beneficial for pricing and after-sales support,” says Ivan Mandiri, technical division supervisor at MSP Film Equipment in Indonesia. His company acquired Master Prime lenses through the ARRI CPO programme. “We also feel assured because the pre-owned lenses have undergone meticulous quality control by ARRI.”
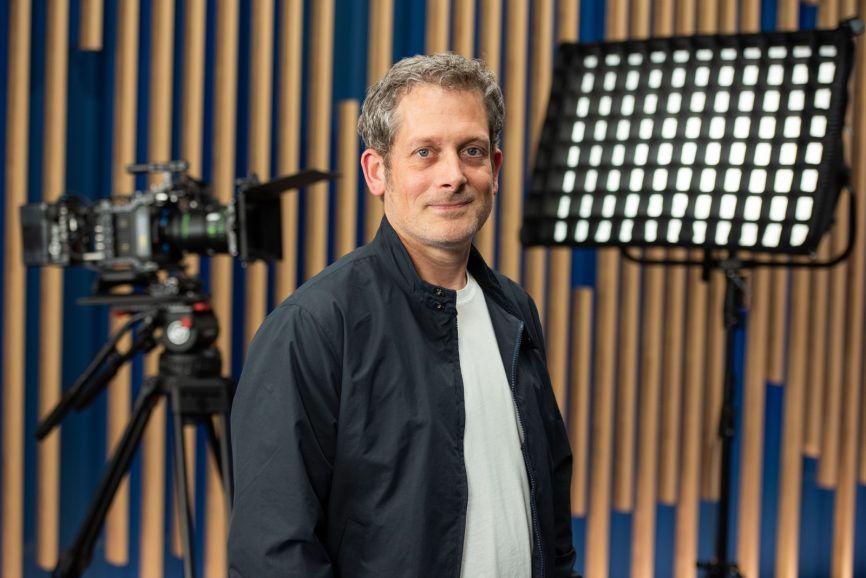
ARRI partner bebob also attaches great importance to sustainability. In addition to reducing emissions throughout the entire production cycle, the German manufacturer builds repairable batteries – older cells that are no longer efficient can be replaced with new ones. This unique approach not only reduces waste and the carbon footprint, but also guarantees cost-efficiency.
Retrofitting offers another solution for extending product life. Broadcast studios and theatres are replacing halogen lights with energy-efficient LED lighting that meets camera capability and varying colour temperatures. However, halogen lights still in good condition need not be discarded. Coemar provides ReLite LED-Kits for conventional light sources, allowing them to be cost-effectively retrofitted to LED. “We can retrofit a broad spectrum of Fresnel lights and profile spots, up to 2,000W, from various manufacturers,” says Claas Ernst, managing director of VisionTwo, Coemar’s German distributor and service partner. ReLite Kits are available in Tungsten, Daylight, and VariWhite colour temperatures for all light types. Profile spots can even be retrofitted with a Multi-Colour ReLite Kit LED Engine that reproduces the entire colour spectrum.
VisionTwo has equipped NDR, MDR, Bavaria broadcast studios, and the Salzburg Festival with ReLite Kits. Recently, ReLite Kits have also become available for 5kW fresnels, which remain in high demand among repertory theatres. “The installation of ReLite Kits is straightforward because the manufacturer developed adaptable hardware solutions for conventional spotlights,” concludes Ernst. “Retrofitting an existing light costs about 20% to 50% less than buying new.”
–
Words: Birgit Heidsiek